GENERALLY SPEAKING MOST PEOPLE DON’T ASSOCIATE CUSTOM WITH COST EFFECTIVE, BUT THEY DON’T HAVE TO BE MUTUALLY EXCLUSIVE.
Most of the time, if anything is custom it costs more than a standard counterpart. However, in many cases, knowing what to ask your cable manufacturer will help you keep costs in line. It’s no different with custom design cables or custom cable assemblies.
What are custom design cables and cable assemblies?
Let’s start with the basics and define what a custom design cable or cable assembly is by defining what it isn’t. If you can find the cable or cable assembly you need in stock, it’s not custom. Companies typically don’t stock custom items because they aren’t purchased often enough to justify the cost of carrying the inventory. So, if you’ve searched and can’t find the cable or cable assembly you need off-the-shelf, odds are you need a custom product.
In the immortal words of Douglas Adams, “Don’t panic!” Just because you need something custom doesn’t mean you need to be robbed. Most times the only difference between a standard product and custom product are a few minor, but important, details. Making those changes doesn’t always have to be expensive.
Getting Started on Custom Design Cables
When you can’t find what you need, start looking for a custom product by describing it using standard terms. For example, we make USB cables for the retail security industry that prevent thieves from cutting the cable and running off with a new cell phone. These cables aren’t that different from a standard product except for one very important feature: If someone tries to cut them, they can’t—at least not very easily. While this feature increases the price, it is NOT by factors of 2, 3, or 4. Since we extrude cable, it’s easy for us to include cut resistance in the design phase. This would only add cost for the added material, and not a penny more because we feel like it.
More Complex Custom Design Cables
If the cable you need is a bit more complex, you can describe it as a combination of standards to get your needs across. We recently created a coil cord for an off-the-road vehicle company. The cable was custom, but it was clearly described as a combination of RS-232, USB, and 12Vdc power. All three are
very standard but generally not found in one cable, not to mention in the form of a coil cord. However, when defined by the standard items, it was quite easy to understand what the client needed.
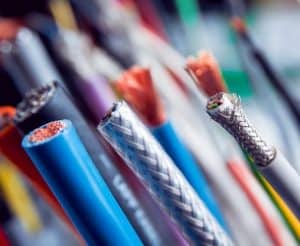
Don’t worry if you don’t know the “standards,” like RS232, USB, OBDII, SAE1850, ISO914 L, CAN Bus, UL8750, and so on. You don’t need to be a standards expert; a good custom cable manufacturer will know that stuff and can guide you. Just describe the items you want to connect, or better yet, describe the kinds of cables you want to combine. Then you can ask what standards the manufacturer will design and build the cable to, so you can decide if you really need that standard. Often the only difference between a cable that meets a “standard” and one just like it that doesn’t is nothing but a testing house approving the cable. If you don’t need this seal of approval, don’t pay for it. If you do need it, then it’s a good idea to spend the extra money. Either way, make sure you know so you can make an informed decision.
How much cable do you need?
Last, don’t be fooled into thinking a custom design cable automatically means producing tens of thousands of feet at a time. A good custom cable company should be able to extrude runs of custom cable of no more than a few thousand feet if necessary. Cable extrusion is a fast process, often running at speeds of 3-5 feet per second. It’s not easy to do small runs, but it is not impossible. Many companies just don’t want to do small runs because they aren’t set up for them. Find a company that is and your costs will be much lower.
Conclusion
Custom cable design doesn’t automatically mean you have to break the bank to pay for the solution you need.
Get in touch with the team at Meridian Cable when you are ready to see how we can help you stay in budget on your next custom cable project