CONDUCTOR GAUGES FOR CUSTOM DESIGN CABLES
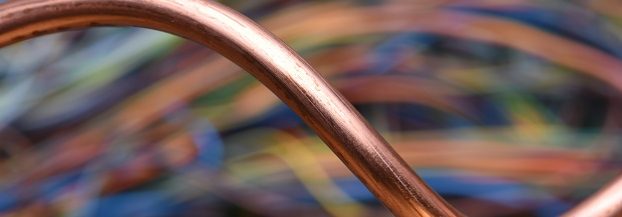
THE RIGHT GAUGE CONDUCTORS ARE KEY TO MAKING YOUR CUSTOM DESIGN CABLES AS EFFECTIVE AS POSSIBLE.
It’s no secret that creating custom design cables is the best way to ensure your product or equipment meets all of your specifications. Because the conductor gauge directly affects the flow of electricity or signal through the final product, the choice you make is extremely important. Choosing the wrong gauge can result in a less efficient cable that might lead to unnecessary costs. A reputable custom cable manufacturer will help you make the right choice and get the most successful outcome.
Cable Conductor Types
There are two main types of wire: solid and stranded. Solid conductors are a single, solid strand, usually made of copper. Stranded conductors are made up of smaller strands of copper that are twisted together to create a larger conductor. The main difference is that a stranded conductor is better able to withstand bending than a solid conductor. Additionally, solid conductors are less expensive to produce than stranded.
Why Size Counts with Custom Design Cables
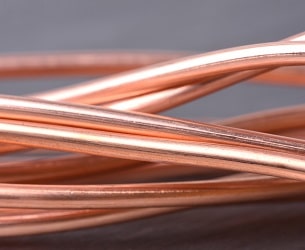
For both types, the overall size of the conductor affects the flow of signal and electricity. Signal or electricity flows through larger gauge conductors more easily than it does smaller gauges. We refer to how easily the signal flows through the conductor as resistance. A wire with a conductor gauge that is too small is not providing the right amount of signal to the equipment it is powering. This could result in the equipment not functioning as it should. A too-small conductor gauge could also cause the wire to overheat, which may cause it to fail.
So…Larger Gauges Are Better?
While working with a larger conductor gauge seems like the safest bet, it’s not always the best option for your project. Larger gauges are able to accommodate more current, but they can be more expensive than all but the smallest gauges. In the end, the best gauge for your project is the one that closely matches your equipment specifications. Having an in-depth discussion with your cable manufacturer’s design team about the needs of your product is the most effective way to make sure you end up with a custom cable that functions as expected.
Gauge & Wire Length
When determining the gauge of conductors for custom design cables, the circumference isn’t the only consideration. The final length of the wire also affects the amount of resistance the current experiences. The longer the wire the more resistance there is, which weakens the signal. For longer cables, it may be necessary to use a larger gauge to counteract the resistance caused by the length.
Conclusion
Choosing the right gauge can be a complex process that includes a thorough understanding of the final cable’s uses, length, voltage, and signal type, as well as many other considerations. Working with a cable manufacturer you trust can make all the difference to the success of the final product. The Meridian Cable team has extensive experience with a wide range of custom cable design projects. When you are ready to discuss your next custom cable, please contact us. We look forward to talking with you.
COST EFFECTIVE CUSTOM DESIGN CABLES
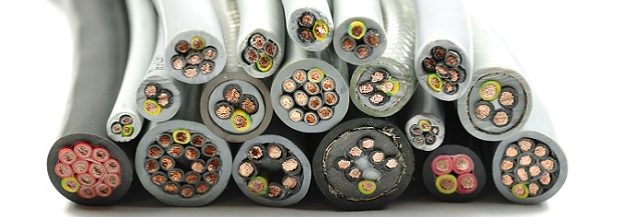
GENERALLY SPEAKING MOST PEOPLE DON’T ASSOCIATE CUSTOM WITH COST EFFECTIVE, BUT THEY DON’T HAVE TO BE MUTUALLY EXCLUSIVE.
Most of the time, if anything is custom it costs more than a standard counterpart. However, in many cases, knowing what to ask your cable manufacturer will help you keep costs in line. It’s no different with custom design cables or custom cable assemblies.
What are custom design cables and cable assemblies?
Let’s start with the basics and define what a custom design cable or cable assembly is by defining what it isn’t. If you can find the cable or cable assembly you need in stock, it’s not custom. Companies typically don’t stock custom items because they aren’t purchased often enough to justify the cost of carrying the inventory. So, if you’ve searched and can’t find the cable or cable assembly you need off-the-shelf, odds are you need a custom product.
In the immortal words of Douglas Adams, “Don’t panic!” Just because you need something custom doesn’t mean you need to be robbed. Most times the only difference between a standard product and custom product are a few minor, but important, details. Making those changes doesn’t always have to be expensive.
Getting Started on Custom Design Cables
When you can’t find what you need, start looking for a custom product by describing it using standard terms. For example, we make USB cables for the retail security industry that prevent thieves from cutting the cable and running off with a new cell phone. These cables aren’t that different from a standard product except for one very important feature: If someone tries to cut them, they can’t—at least not very easily. While this feature increases the price, it is NOT by factors of 2, 3, or 4. Since we extrude cable, it’s easy for us to include cut resistance in the design phase. This would only add cost for the added material, and not a penny more because we feel like it.
More Complex Custom Design Cables
If the cable you need is a bit more complex, you can describe it as a combination of standards to get your needs across. We recently created a coil cord for an off-the-road vehicle company. The cable was custom, but it was clearly described as a combination of RS-232, USB, and 12Vdc power. All three are very standard but generally not found in one cable, not to mention in the form of a coil cord. However, when defined by the standard items, it was quite easy to understand what the client needed. 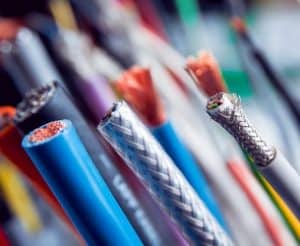
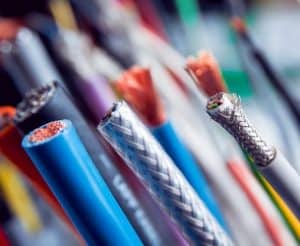
Don’t worry if you don’t know the “standards,” like RS232, USB, OBDII, SAE1850, ISO914 L, CAN Bus, UL8750, and so on. You don’t need to be a standards expert; a good custom cable manufacturer will know that stuff and can guide you. Just describe the items you want to connect, or better yet, describe the kinds of cables you want to combine. Then you can ask what standards the manufacturer will design and build the cable to, so you can decide if you really need that standard. Often the only difference between a cable that meets a “standard” and one just like it that doesn’t is nothing but a testing house approving the cable. If you don’t need this seal of approval, don’t pay for it. If you do need it, then it’s a good idea to spend the extra money. Either way, make sure you know so you can make an informed decision.
How much cable do you need?
Last, don’t be fooled into thinking a custom design cable automatically means producing tens of thousands of feet at a time. A good custom cable company should be able to extrude runs of custom cable of no more than a few thousand feet if necessary. Cable extrusion is a fast process, often running at speeds of 3-5 feet per second. It’s not easy to do small runs, but it is not impossible. Many companies just don’t want to do small runs because they aren’t set up for them. Find a company that is and your costs will be much lower.
Conclusion
Custom cable design doesn’t automatically mean you have to break the bank to pay for the solution you need. Get in touch with the team at Meridian Cable when you are ready to see how we can help you stay in budget on your next custom cable project
HOW TO WORK WITH A CABLE ASSEMBLY MANUFACTURER WHEN YOU HAVE A TIGHT BUDGET
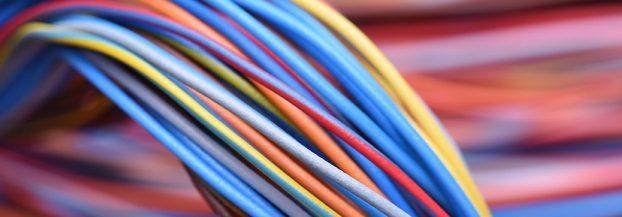
A CABLE ASSEMBLY MANUFACTURER HAS MANY OPTIONS AVAILABLE THAT CAN HELP YOU STAY IN BUDGET AND GET A CUSTOM CABLE THAT IS RIGHT FOR YOUR SITUATION.
Having an unlimited budget to work with when designing a custom cord might seem like the best way to get the perfect end product, but that type of situation is rare. In most cases, budget is a concern. The good news is your cable assembly manufacturer should be able to help you balance the cable’s functionality with cost.
Good Communication Saves Money
This may seem like common sense, but make sure you are sharing as much information with your cable assembly manufacturer as possible in the planning and design stages of your project. Having clear specifications about how and in what environment the finished product will function gives the design team a thorough understanding at the outset. This can translate to a cable assembly that meets the needs of the equipment and environment with fewer revisions or surprises late in the project.
Talk Materials with Your Cable Assembly Manufacturer
Armed with complete technical specifications and a good understanding of the environment where a finished cable assembly will function, the design team is able to select the optimum materials to create a solution that operates as expected. At its most basic, a cable is made up of a conductor, connectors, jacketing, and insulation. Each can offer an opportunity for cost savings with some careful thought.
Conductors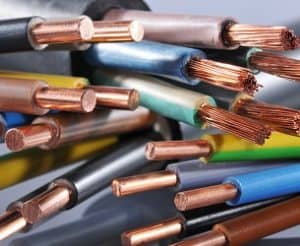
Obviously, the conductor material should be selected based on the type of signal and how long the cable is expected to be in use. However, with so many options when it comes to size, material, and plating, a cable assembly manufacturer can make recommendations that address cost concerns without compromising on functionality. For example: In many cases, a smaller conductor is less expensive. Choosing the smallest conductor that will transmit the signal or power allows you to get the functionality you need without the unnecessary expense of a larger conductor. Though, in some cases, a smaller conductor is actually more expensive to produce, so it’s doubly important to discuss options with your cable’s design team.
Connectors
All cable assemblies connect to some sort of equipment or power/signal source. Because the section of cable that leads to the connector is a common point of failure due to stresses, it’s important to select the right type of connector for the job. While an overmolded cable offers more durability in many cases, it may make more sense to use a connector that can be repaired by a technician. Understanding the needs of your finished product allows you and your cable assembly manufacturer to make the right decision before producing a cable that doesn’t fit your needs.
Jacketing & Insulation
The environment where a cable assembly will be used often dictates what type of jacketing material or insulation is used in the finished product. Different materials are more suitable for cables that are exposed to extreme heat or cold, moisture, or stresses. More expensive materials for jacketing aren’t automatically better for every environment. In many cases, choosing a more costly material that is unsuited for the environment can be a waste of money and compromise the function or service like of the cable.
Conclusion
Good planning, open communication, and thoughtful selection of materials is the great way to save costs when creating a custom cable with a cable assembly manufacturer. If you are ready to talk about your next custom cable project, contact the team at Meridian Cable. We’d love to discuss your options.
CUSTOM CABLE ASSEMBLIES WITH STANDARD CABLES
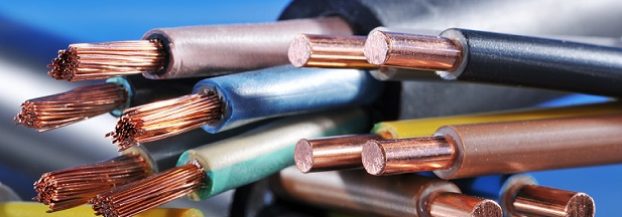
WHEN DESIGNING CUSTOM CABLE ASSEMBLIES FOR YOUR PRODUCT, IT’S NOT ALWAYS NECESSARY TO START FROM SCRATCH.
Custom cable assemblies are designed and extruded for products or equipment when an existing cable does not meet the needs of the application. While stock cable can be inexpensive and easy to source, it doesn’t make sense if it simply doesn’t do the job required or is not as durable as it needs to be to withstand environmental conditions. In many cases, custom cables are a great way to make sure all your needs and specifications are met.
Cost is always a consideration whether you are dealing with custom or stock cable. Many perceive that “custom” means a higher price tag, but this doesn’t have to be the case. There are circumstances when a custom cable can even save money. For example:
- Low Durability – A stock cable that doesn’t quite offer the durability for your application is going to need to be replaced more often. A custom cable more suited to the requirements and environment would need to be replaced less frequently.
- Many Cables for One Piece of Equipment – One custom cable that meets all your needs is easier to install, maintain, and replace than multiple stock cables.
- More Cable than You Need – Using stock cables means you sometimes have to pay for a more expensive option than you actually need. A custom cable eliminates that need because it is designed to meet the specifications of your equipment.
- Creating a Cable from the Ground Up – There are circumstances when incorporating an off-the-shelf cable into a custom cable assembly saves time and money.
Making Smart Design Choices with Stock Cable
Commissioning a custom cable doesn’t mean you have to start from scratch by designing a completely new cable. If a stock cable is nearly perfect for your application, it’s possible to make some changes with a design based on the existing cable. These changes could include adding a tougher jacketing material or reproducing the cable with more flexibility or a different gauge that is not currently available.
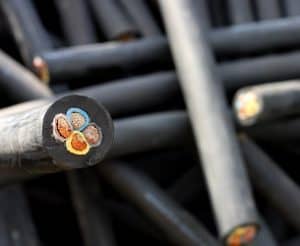
Depending on the specifications of your product or equipment, you may need a custom cable assembly that combines multiple cables into one to save space. By combining these cables, the engineer can take advantage of different gauges and cable types – which may include stock cables – to create a streamlined solution that is tailored to your needs and specifications.
Talking with an Expert Wire & Cable Manufacturer
Off-the-shelf cables can be a great choice if there’s an existing model that matches the specifications for your product or equipment that is able to hold up to the environment where it will be used. But if a stock cable doesn’t meet your needs or is only “close enough,” talking to a wire and cable manufacturer might be the logical next step. During your initial discussion, make sure you clearly communicate how the finished cable needs to perform. If you are currently using an existing cable, share any frustrations or limitations you are experiencing. This will allow the engineering team to gain a full understanding of whether incorporating an off-the-shelf cable into your custom cable design makes sense.
An experienced manufacturer of custom cable assemblies, like Meridian Cable, can make recommendations that address any issues you are having with stock cables. They are also able to help you make the best choices when considering incorporating existing cables into your custom solution.
DETERMINING THE SHAPE OF A CUSTOM COIL CORD
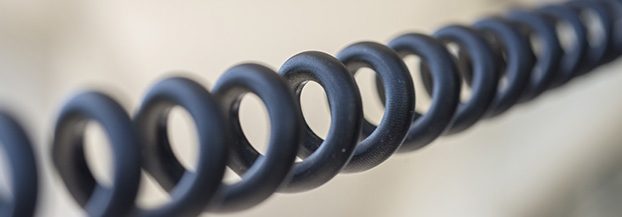
THE SHAPE OF A CUSTOM COIL CORD IS ONE OF THE MOST IMPORTANT ELEMENTS WHEN DESIGNING THIS TYPE OF CABLE.
Custom coil cord is known for its flexibility, making it the perfect choice for applications that require a cable that can stretch and retract without putting additional stress on the wire. It has the ability to extend beyond the natural length at rest, which can be a real space-saving feature. These cords are flexible beyond simple extending and retracting in that they can also be pulled, bent, and twisted without experiencing the metal fatigue of a straight cable.
Coiled cable can be used to carry electrical currents as well as data and signal for telecommunications applications. This versatility makes coil cords ideal for use in environments that are often too rough for non-coiled cable. Coil cords are used in everything from equipment on industrial and construction sites to portable electronics, like sound equipment. With so many applications at so many different sizes, the shape of your custom coil cord is key to its successful performance.
Requirements Determine the Shape of Coiled Cable
If you’ve ever seen a telephone cord, you’ll recognize the shape of a coiled cable – curled in the middle with a section of straight cable at each end. While the specifications of the straight sections are important to the overall function of the cable, it is the coiled section that provides the cord with its unique benefits. The retracted length of the cord is how long it is at rest. This is the most common way to specify how long the cord should be. However, it is also necessary to communicate the full length the cord must extend to, so the engineers at your custom cable manufacturer are able to get a full understanding of the requirements of your cable.
The coil’s diameter is a key measurement when determining how far a custom coil cable should extend. In general, a coil with a larger outer diameter with stretch farther than a coil with a smaller outer diameter. When discussing your cable’s specifications with your cable manufacturer, retracted length, extended length, and outer coil diameter will provide a good starting place for the designer regarding the cable’s physical shape.
Fine-Tuning a Cable’s Performance
While you may be able to get pretty close to the final shape of your custom coil cable on your own, the cable’s construction and materials are best selected with the help of an experienced wire and cable manufacturer. Selecting specific fillers and jacketing materials can also add durability to the finished cord. Depending on how tough you need your cable to be, materials can include: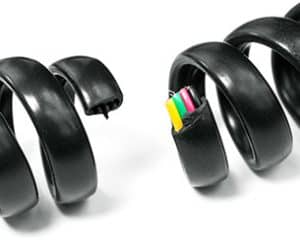
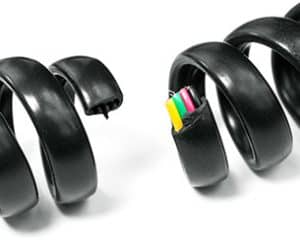
- PU
- PTEE
- TPR
- SVO
- SJOW
- Kevlar®
- Spectra®
- Teflon®
An expert cable manufacturer like Meridian Cable, learns everything they can about how your coil cable needs to function. This allows them to make the best recommendations on the materials and physical shape to ensure the finished cable meets the needs of your product or equipment. Rest assured that no matter what your application, a custom coil cord solution can be designed and produced to perfectly match your specifications.
No comments:
Post a Comment
THANKS FOR VISIT
Note: Only a member of this blog may post a comment.